The ROI on food manufacturing engineering testing, audits and other compliance measures.
- chrisbunyan8
- Apr 27, 2022
- 4 min read
Updated: Apr 29, 2022
The next few months are going to put immense strain on food and beverage manufacturers, and not only due to increased demand due to the summer season, rising energy costs and driver shortages. They also face the constant spectre of failed inspections, or worse still, product recalls and fines that hit the headlines.

Regulatory restraints on food safety now run alongside industry-specific enforcement regimes, cross-agency and cross-government guidance, and the best practice standards created by partnerships between the food sector and consumer bodies (UK and internationally).
It creates a complex pattern of compliance and a lot of ways to trip up! How can putting an even greater focus on manufacturing engineering testing and audits guard you against many of the risks you face?
Food safety and reputation management
According to this 2021 food security report released by the UK government, “across England, Wales and Northern Ireland the percentage of establishments that are found on inspection to be broadly compliant or better with food hygiene law has increased from 89% in FYE 2015 to 90.4% in FYE 2020. In Scotland, compliance with food hygiene increased from 88% in 2015/16 to 93% in FYE 2021.”
Yet, there appears to be an increasing number of food incidents in the UK.
A quick check on the latest products listed on the Food Standards Agency alerts page certainly shows there is no room for complacency. Especially when major brands like Ferrero and Tesco have been forced to issue product recalls recently.
It is the sort of issue that dents any company’s reputation, and order books. For smaller food manufacturers, it could be something they never recover from.
The escalation in food recalls could be due to a range of factors. This includes rapidly advancing technology that can detect even trace amounts of pathogens. It is also likely to be linked to both the increasing regulatory control placed on this sector and voluntary reporting by food businesses.
Also, there are still companies overlooking vital steps in health, safety, quality and environment (HSQE) management. Leaving workers and local environments at risk, as well as putting the company’s reputation ‘on the line’ when it comes to product safety standards.
Steps to managing risk in food manufacturing
Whatever type of food and beverage niche you operate in, year-round vigilance is key. Also, being ready to reinforce that vigilance even when demand for output is at its highest, and you have many other priorities to juggle.
The fundamental requirement is delivering scheduled and documented work to manage risk, protect staff, and ensure products can do no harm to end-users. This largely revolves around investment in frequent manufacturing engineering checks, upgrades and cleans. Nothing should be left to chance or ignored until the pressure dies down.
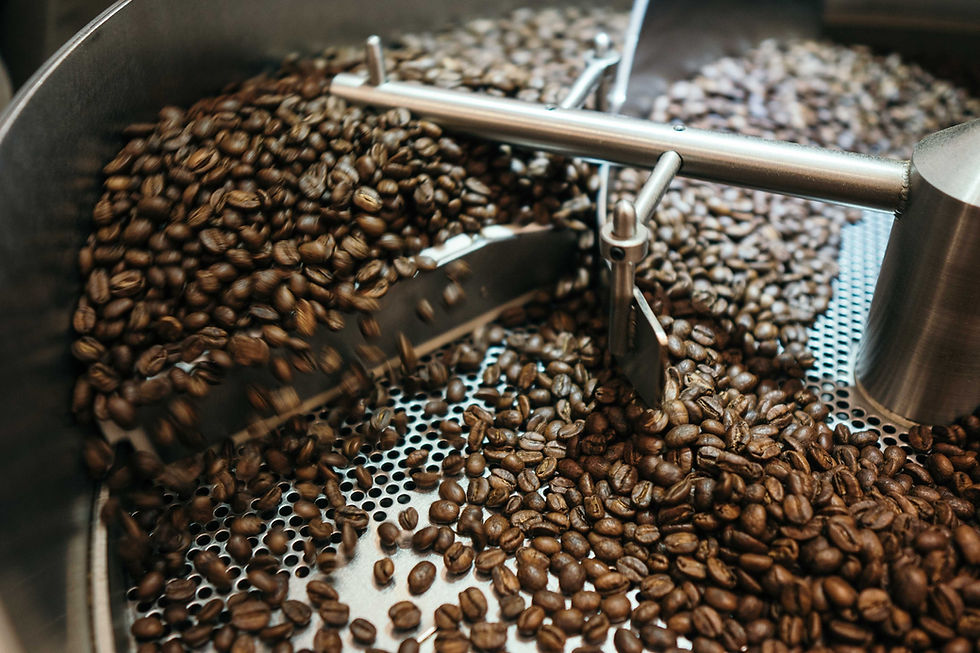
ROI on manufacturing engineering experts
Bringing in manufacturing engineering specialists for inspections, testing and asset surveys can become an invaluable investment. It frees your in-house team to focus on their normal, daily tasks and priorities, and can often help you to identify issues early enough to nip problems in the bud.
It also provides you with clear accountability, and all the documentation needed to prove compliance. Or, to track plant repairs, upgrades and improvements connected to HSEQE requirements.
To some degree, the question should be: Can you afford not to engage experts in evaluating, testing and maintaining your manufacturing plant and equipment? Apart from the issues mentioned at the start of this article, oversights that impact food safety can leave you having to action an unscheduled shutdown.
Despite regular engineering scheduling and the advent of advanced technology, there is evidence that unexpected downtime costs UK manufacturers as a whole 180 billion every year. Why chance being part of that shocking statistic?
Inefficient and outdated manufacturing machinery
Going beyond what is demanded to remain HSQE compliant can be invaluable. Particularly with regard to engineering audits to detect weaknesses, defects, inefficiencies or issues that could eventually lead to health, safety or food hygiene problems.
This is something often best left to independent engineering specialists, with the ability to do lifecycle analysis as part of thorough inspections. They also need to be innovators, armed with solutions and not just red flags!
One of the challenges many companies have in matching modern-day food safety standards is that their plant consists of legacy equipment, and machines that struggle to cope with current capacity and control systems.
It’s also the sort of manufacturing machinery that’s difficult – if not impossible – to integrate into the latest manufacturing technology, including software and sensors that constantly gather and analyse operational data. This potentially leaves you with blind spots that only become apparent when a product is already in the public realm.
This is where Engex can be invaluable. We have the knowledge, strategies and experience to bring about cost-effective manufacturing engineering revitalisation, transforming production lines into more streamlined, efficient and reliable systems.
We also offer asset surveys and other services to drill down on compliance risk areas.
For relatively little cost, this sort of manufacturing engineering excellence has the potential to protect you against millions of pounds of potential losses and to avoid the food safety infringements that could put your entire business at risk.
Comments