3D Printing in Engineering
- chrisbunyan8
- Jan 23, 2023
- 4 min read
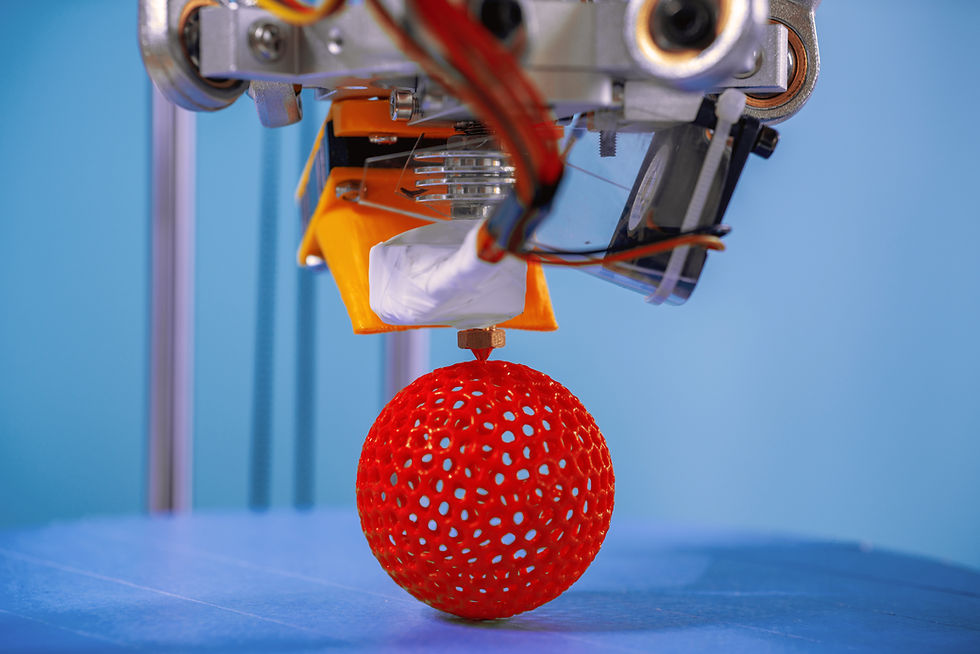
One of the most transformational developments of recent times is the technology and skills capable of precision engineering parts using 3D printing.
It has clearly substantially impacted lead times – and therefore machinery downtime – as well as providing significant cost savings for manufacturing and engineering companies.
The advantages of 3D printing in engineering have been thrown into sharp relief by current supply problems too. Brexit and strain on road transport logistics have conspired to cause costly delays in the arrival of basic parts for manufacturing equipment.
These frustrations can be greatly eased by not only using 3D printing to short-circuit supply chains but also creating spare part 'stock' without overburdening your storage or capital expenditure. This article explains how that works.
What is 3D printing in engineering?
The normal process involved in commissioning spare parts for manufacturing equipment involves working with a specialist supplier, who uses CAD technology and precision engineering equipment to fulfil medium to large production runs. Ordering in volume manages unit costs, including prototype set-up and tool manufacturing.
One of the big drawbacks of this traditional supply system is that spare parts are not always needed in large numbers. Storing them can take up valuable space while ordering them ‘ad hoc’ can lead to higher costs, and the need to plan well ahead to manage maintenance and repairs.
A solution has been found using specialist 3D printing for rapid prototyping.
3D modelling technology now enables an infinite variety of specifications to be programmed in, to achieve the perfect part. Then, objects are created layer by layer using the three-dimensional software to craft a wide range of materials into the desired shape, size and tensile outcome.
Many 3D printers use Fused Deposition Modelling (FDM), with heat and thermoplastic filaments to integrate the layers. Other types include Stereolithography (SLA) printers, incorporating a UV laser to cure photo-reactive epoxy resin layers. A further technique is Selective Laser Sintering (SLS) using a high-powered laser to fuse tiny polymer powder particles together.
From this variation in methodology comes the ability to precision engineer even heavy-duty objects with 3D printing equipment. As well as parts with complex geometries and internal structures produced relatively quickly.
When the 3D printer is on-site, the item can be immediately available for use.
Creating spare parts stocks for manufacturing equipment

One of the challenges of modern manufacturing management is holding a sufficient inventory of spare parts, without tying up too much capital or precious storage room.
The way 3D printing works enables parts to be held ‘virtually’ ready to call off when required. This digital library of the parts can also be created where they are needed, which is particularly valuable for companies operating multiple sites.
As 3D printing parts is a highly automated digital system, you can hold ‘virtual stock’ of even the most rarely required parts. As well as enabling swift production of your most needed objects.
Benefits of spare parts created by 3D printing
Compared to alternative ways to source low-volume production of parts, the cost of 3D printing is highly attractive.
This is particularly true as this is the ideal way to carry out R&D projects. You can seamlessly commission and test new parts on-site, using this rapid prototyping equipment.
It is possible to address problems and find solutions seamlessly, using 3D-printed objects. The reduction in lead times for runs alongside an ability to expose flaws swiftly, further cutting wasted time and costs.
Also, 3D printing is the ideal solution for reverse engineering parts quickly and cheaply.
However, for many companies, the most compelling reason to invest in 3D printing technology is to gain far greater control over part production. Instead of relying on overseas suppliers, and all the complexities they now involve, low-volume runs can be created quickly - often in hours.
The process takes longer if a metal is involved, as Direct Metal Laser Sintering (DMLS) involves programming the system to operate a high-power laser beam, which then melts and fuses metallic powder layers. This industrial 3D printing process can reduce lead times to a matter of days though, compared to weeks.
Types of materials which can be used for 3D printing
Potentially the biggest misconception about 3D printing in engineering is that it is limited in the types of objects and structures it can create. The most common type of part printed using 3D technology is one made of a type of plastic. However, the latest technology and skills (as mentioned above) have greatly expanded the possibilities for this form of rapid prototyping.
This includes engineering metal parts this way – from gold to stainless steel and titanium – or crafting objects made from graphite, graphene, carbon fibre and of course paper, cards and fabrics.
Keep in mind that the speed and cost advantages of 3D printing make it much easier to test parts. Enabling you to possibly switch to ones made from lighter and cheaper materials without impacting performance values.
Are there disadvantages to 3D printing in engineering?
The benefits of using this method to produce – and store – parts for manufacturing equipment are impressive. However, the challenge is to use 3D printing technology with sufficient expertise to set and maintain high-quality standards and to meet exacting industry specifications consistently.
The software used can only go so far in meeting these objectives, and making your parts 100% reliable and repeatable can depend on having access to skilled engineering services.
Related Information
Find out more about 3D printing and how else Engex can assist you with your engineering projects.
Comments