

Corporate HSQE Management, Compliance & Testing
Within this division of Engex, we provide a comprehensive suite of services to manufacturing clients across all markets and industries, that cater for all of your planning and ongoing requirements. These services include:
Consulting
Advisory Services
Testing & Compliance
Plant Inspections
Asset Management
Condition Reports
Training
Audits & Internal Accreditations Support
Budget Planning
Asset Lifecycle & Succession Planning
CapEx Investment & Maintenance Investment Guidance

Approach and value of compliance and testing
Testing & Compliance
Mechanical & Electrical testing are a standard and essential part of any design and manufacturing process. Whether it is characterising the properties of materials or providing validation for final products, ensuring safety is the primary mission of all M&E testing. Testing also plays a crucial role in ensuring a cost-effective design as well as technological evolution and superiority.
Origins of test requirements
The test methodologies required are characteristically specified on drawings of the parts, which means that the testing responsibility falls to the manufacturer contracted for that part.
Testing requirements are not always set by governing bodies; experienced design and manufacturing teams also understand the value of testing to validate models, make improvements, and increase parts' overall quality. When faced with the cost and time implications of testing, it may seem like this process is expensive. However, it is an excellent place to start when it comes to reducing costs as unanticipated failures when the parts are in service have higher cost and time implications.
Common types of testing
The process starts with a review of the drawing or part specification to identify appropriate test methods, which can include:
Model generation and validation
When it comes to streamlining the design process, solid modelling of components and assemblies, along with Finite Element Analysis (FEA), are excellent tools. Often the purpose of mechanical testing is to generate the data required by these FEA programs to generate the initial component models. FEA models do not guarantee accurate results, so we believe the most practical approach is to:
-
Develop a robust model from the materials testing data for the material
-
Perform FEA to determine theoretical stress levels and locations, and use product qualification testing or materials testing on component cut-ups (First Article Inspection) to validate the FEA model.


Tensile Testing
Raw material lots are likely to vary, so tensile testing of each lot ensures that it meets minimum strength and ductility requirements. Although material suppliers are equipped to handle these tests, they recommend using a third-party laboratory test as independent and additional confirmation. Engex can provide all of this for our clients. Confirming that raw material is within acceptable limits is one of the easiest and most cost-effective assurances against future problems.
Chemical Analysis
Chemical analysis is also essential for both material and product manufacturers as it identifies the contents and quality of materials used in manufacturing and product development. During the early stages of the product development process, it is essential to verify materials to avoid any in-service failures.


Hardness
Hardness testing is required after production and also where heat treating is needed to verify conformance. Like tensile testing, this is a speedy and inexpensive testing option and does not usually require the final part to undergo destructive testing
Fatigue Testing
In most applications, the objective of fatigue testing is to develop a fatigue strength curve that characterises the material's ability to resist cyclic loading over fluctuating stress levels or to establish the operating conditions when fatigue would not be experienced in the component's lifetime. Once this curve is established, the results are compared to the part design criteria to make sure that the material will enable the component to fulfil its projected life expectancy.
The final part geometry can make it challenging to apply raw material fatigue data due to complex dimensional features such as notches and holes. When this is the case, it is recommended that the final part undergoes fatigue testing. Going a step beyond the previous methods discussed, this may require a more sophisticated test setup and include the destruction of some production parts. The upside to this approach is that not only can a fatigue strength curve be generated, but failure modes will be determined. This knowledge is valuable for design improvements and maintenance schedules.


Fatigue & Fracture Mechanics
Fatigue and fracture mechanics provides data about a material's capability to withstand flaws and the effect on its strength. When it comes to developing maintenance programs and predicting components' service life, fatigue and fracture mechanics testing is an extremely popular tool. Some machine components will inevitably develop cracks in their lifetime. Replacing parts can be too costly and, in many cases, completely unnecessary; the key is to determine the severity of the flaw and recognise when it crosses the line to become a critical matter.
Fatigue and fracture mechanics are made up of many different static and dynamic tests that characterise a material's resistance to crack growth fracture toughness once a flaw has originated. This knowledge of how a material will react under such conditions enables our clients to estimate the components' life. It means that, in some cases, costly repairs can be postponed to a time convenient to schedule the work. Knowing which materials have higher fracture toughness can improve designs and prolong component life expectancy.
Stress rupture & creep testing
Stress rupture is also essential throughout the product lifecycle. It provides critical information for our clients internal engineers, enabling them to prevent failures by giving insights into the effect of long-term stress on materials and products.
Is testing worth the investment?
As product testing often involves specialised test equipment, custom-fabricated fixtures, skilled test engineers, and additional products and materials devoted to testing, it requires organisations' investment. When today's competitive marketplace is considered, this investment can be difficult to justify when budgets are already squeezed at the start of the project. However, it cannot be underestimated that the failure to perform appropriate testing can have devastating consequences that can cost significantly more than the testing itself.
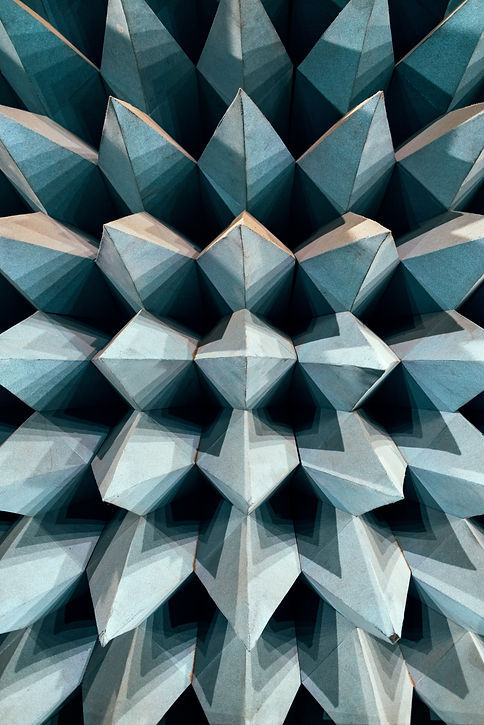


Importance of testing
Engex urge our clients to consider the following problematic outcomes that are brought about by failure to test:
Internal audit
The first and least costly consequence of avoiding testing is the internal discovery of nonconformance through an internal audit or quality check. This is not the worst-case in terms of scenarios as the product has not yet left the premises, meaning the damage is limited. This situation can be alleviated by separating the affected products, evaluating for conformance, and, if necessary, making the required reworks.
Failed audit
Being subjected to findings from an audit is one of the more severe consequences of avoiding testing requirements. Any errors discovered at this stage could be rectified as the affected products can be recalled and evaluated, and reworks and repairs carried out for the products to be re-released. However, as well as the time and cost implications, organisations risk losing a customer's trust and potentially valuable contracts.
Increased costs
If a lack of accurate models are utilised, products and components can often be over-engineered, making them more expensive. Using appropriate models and designing components based on empirical testing data, the lead time for creating components can be reduced.
Product failure
The most costly consequence of not testing is catastrophic product failure. The result of this can be devastating, ranging from product damage to loss of life, and the consequences are permanent with organisations exposed to legal prosecution.
Rest assured that, thanks to our thorough quality checks, we have never suffered a product failure. However, this should be no comfort to the quality engineer whose responsibility is to ensure absolute product conformance at every stage of a project and product lifecycle. By providing strong in-house testing capabilities and partnering with the Engex accredited laboratory, organisations can help to ensure continuity and quality every step of the way.
Working to prevent future failure
Should products fail during the testing phase or in-service, failure analysis is a critical aspect of product development and system improvement, which helps us learn from the past, and helps prevent future failures.
Failure analysis is a multi-faceted, holistic approach to determine how and why a material or product failed. The initial stage of any investigation involves an in-depth discovery phase of the circumstances surrounding the failure and any relevant background information, including environmental factors, type of application, service life, and pertinent design information. Engex's failure analysts then apply a wide variety of analytical methods and tools to inspect the failed part.
Based on the failure analysis process findings, Engex experts provide recommendations and work closely with our clients to find solutions to problems for a diverse range of products and materials. The combination of our materials expertise and our knowledge of what impact the service environment can have on a material or product enables the rapid delivery of comprehensive results.
While identifying the root cause and associated responsibility of any failure are the primary goals, the added value is provided in preventing future occurrences.
Explore Our Other Services
We rely on Engex to deliver engineering solutions to our operations in UK and France and have been incredibly impressed with the service received to date. Their industry knowledge is great and they are often able to advise us on solutions that we wouldn’t have been aware of otherwise. The high standards are maintained regardless of location and on occasion, the same team that we see in UK can be found on site in France later the same week. In particular, the passion that they share with us for positive social impact has been critical to the success of our relationship and they have helped us with many projects that take wasted energy and create free energy and heating for many of our neighbours.
Alain Roussel, Danone